- Joined
- Oct 3, 2019
- Messages
- 679
- Reaction score
- 695
My previous electronic equipment repair projects
Radion XR15:
www.reef2reef.com
Radion XR30:
www.reef2reef.com
Imagine a problem with a connector breaking off the board. Usually not a big deal. Worst case - a couple of torn traces and a new connector. Unless, of course, we are talking about the reef gear. In which case, we have to expect things breaking in new and unusual ways!
This is certainly the case with this AI Hydra light. It was also a mail in service request from a fellow reefer. So I am not exactly sure how this connector came off the board, but... well, take a look at this:
What??? The entire fan circuit is missing. Every. Single. Component.
The area is covered in a thick layer of corrosion to the point you can't tell what is what:
Let's clean up the corrosion and see if there is anything left below it:
Now it is clear that at least some traces and pads corroded away entirely. Both pads from the connector are no longer connected to the board circuit. Looks like there should be a diode, a resistor and some other component.
This is what the fan control circuit should look like:
The third missing component turns out to be a small mosfet. This makes sense, something needs to help the controller switch the fan on and off after all.
Let's get started on restoring the board traces. This time, instead of using the jumpers, I decided to use copper to lay out the new traces.
As you can see, it's not all that bad. Just a couple of runs from the connector pads to link them to the diode and the mosfet, while carefully avoiding unrelated traces in close proximity.
Anyway, we are ready to layout the missing components:
At this point, the fan should work once plugged in. But all of this exposed copper will corrode very quickly again. And then the corrosion will push the new components off the board again.
To solve this, I'll put a good layer of conformal coating over the entire area:
This coating needs to be cured to harden it:
Once hardened, the conformal coating not only protects against corrosion, but also helps to hold my traces to the board.
Now it's time to test if the new fan circuit actually works:
My leading theory on why the damage to the board was so significant is a sequence of events with the old fan failing and shorting first. The short caused a part of the circuit to burn out. You can actually see a small hole in the board right next to the diode where a part of the trace used to be. The short on the board made the black coating to flake off exposing copper on several traces. Copper usually corrodes violently, which might have been enough to push all the circuit components off the board.
Either way, the light is now working and the board circuit is corrosion resistant.
Radion XR15:

Radion Lights Board Level Repair
I enjoy an occasional board level repair. It gives me a new angle to this hobby, which is often very heavy on DIY. In this thread I'm going to post some of my more interesting and challenging repairs, picture heavy, including high magnification microscope imagery. Recently, I got ahold of a...


Radion XR30 complete no light repair
My previous electronic equipment repairs Radion XR15: https://www.reef2reef.com/threads/radion-lights-board-level-repair.774331/#post-8197536 A fellow reefer mailed me their Ecotech Radion for repair service as it's long been out of warranty. The unit turns on briefly before shutting down and...

Imagine a problem with a connector breaking off the board. Usually not a big deal. Worst case - a couple of torn traces and a new connector. Unless, of course, we are talking about the reef gear. In which case, we have to expect things breaking in new and unusual ways!
This is certainly the case with this AI Hydra light. It was also a mail in service request from a fellow reefer. So I am not exactly sure how this connector came off the board, but... well, take a look at this:
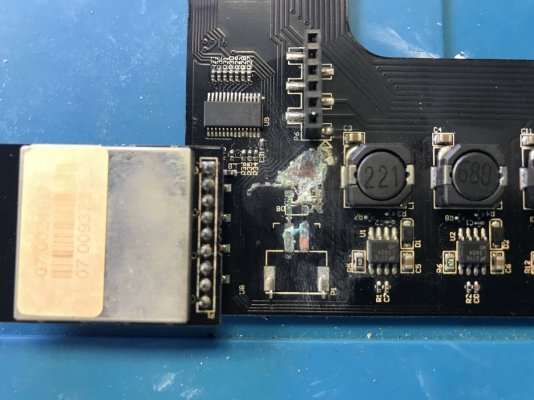
What??? The entire fan circuit is missing. Every. Single. Component.
The area is covered in a thick layer of corrosion to the point you can't tell what is what:
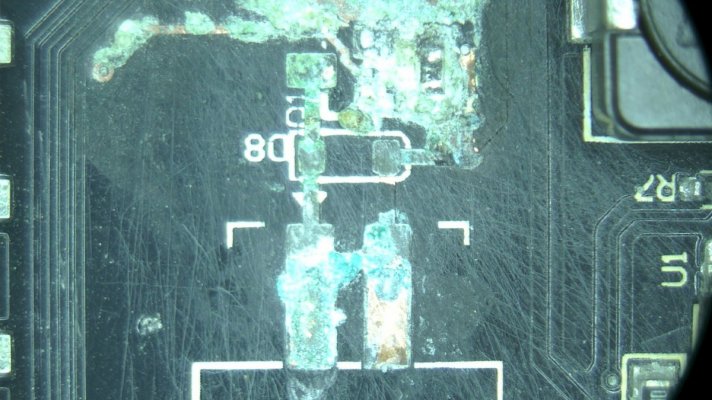
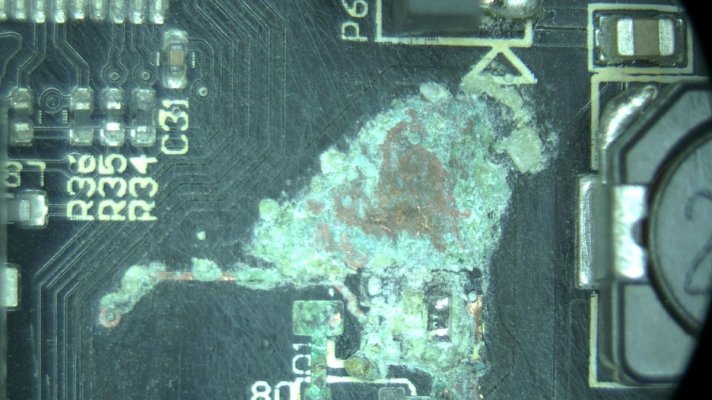
Let's clean up the corrosion and see if there is anything left below it:
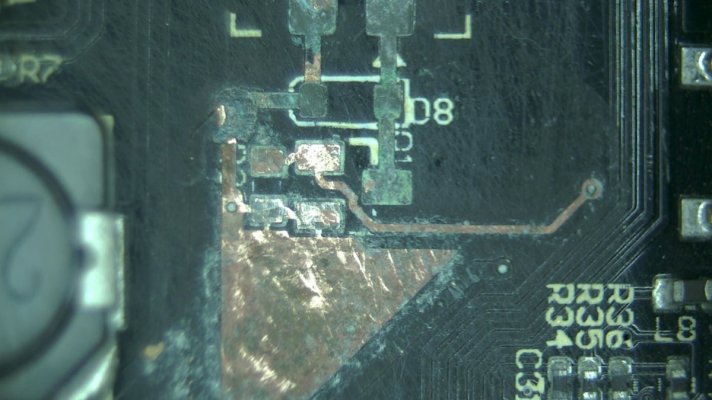
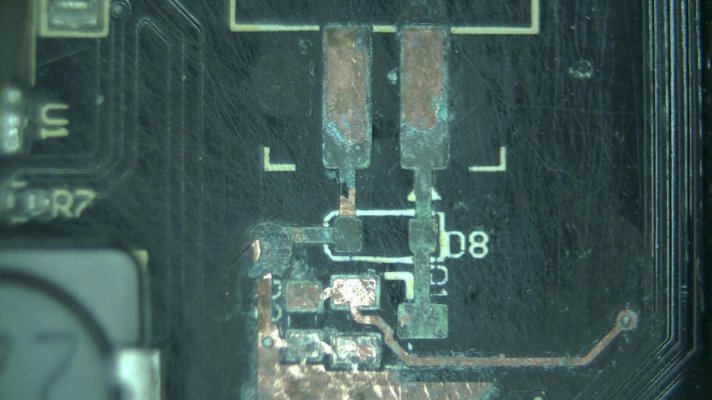
Now it is clear that at least some traces and pads corroded away entirely. Both pads from the connector are no longer connected to the board circuit. Looks like there should be a diode, a resistor and some other component.
This is what the fan control circuit should look like:
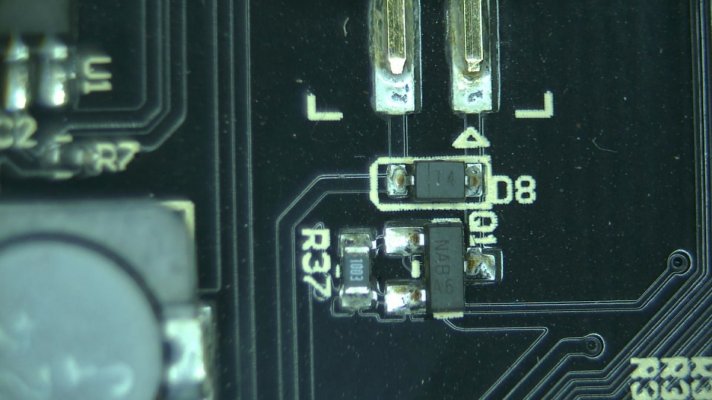
The third missing component turns out to be a small mosfet. This makes sense, something needs to help the controller switch the fan on and off after all.
Let's get started on restoring the board traces. This time, instead of using the jumpers, I decided to use copper to lay out the new traces.
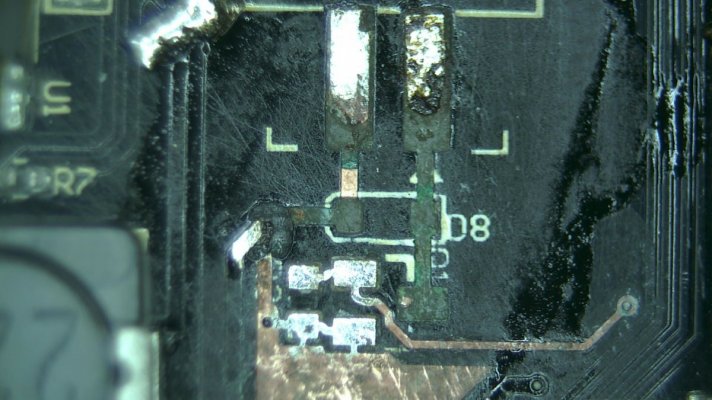
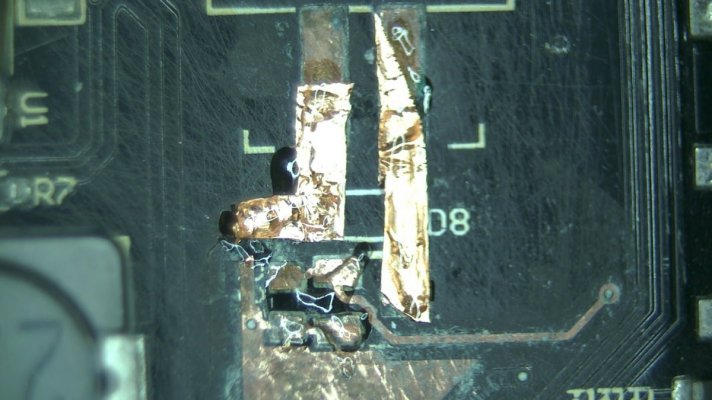
As you can see, it's not all that bad. Just a couple of runs from the connector pads to link them to the diode and the mosfet, while carefully avoiding unrelated traces in close proximity.
Anyway, we are ready to layout the missing components:
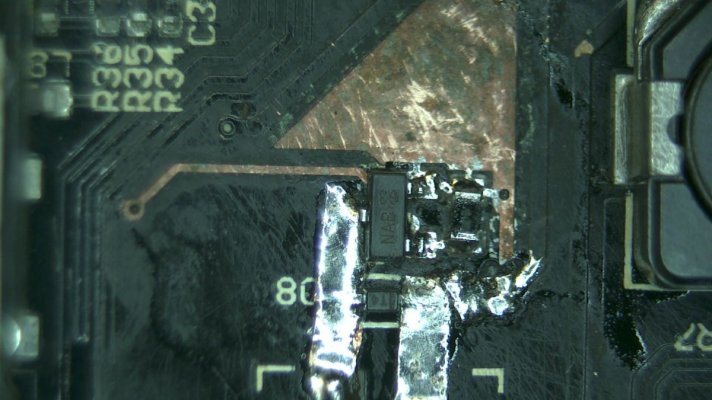
At this point, the fan should work once plugged in. But all of this exposed copper will corrode very quickly again. And then the corrosion will push the new components off the board again.
To solve this, I'll put a good layer of conformal coating over the entire area:
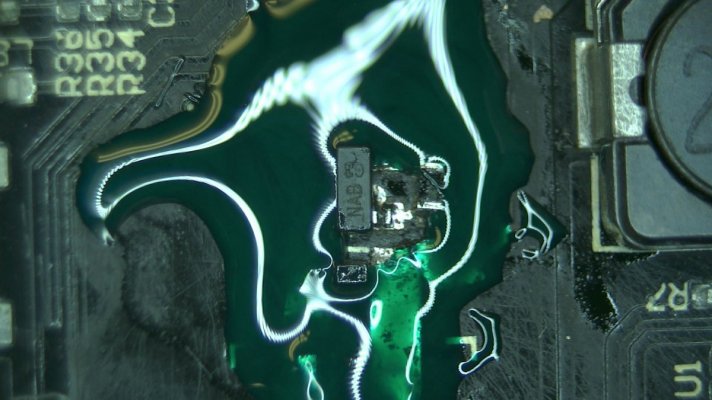
This coating needs to be cured to harden it:
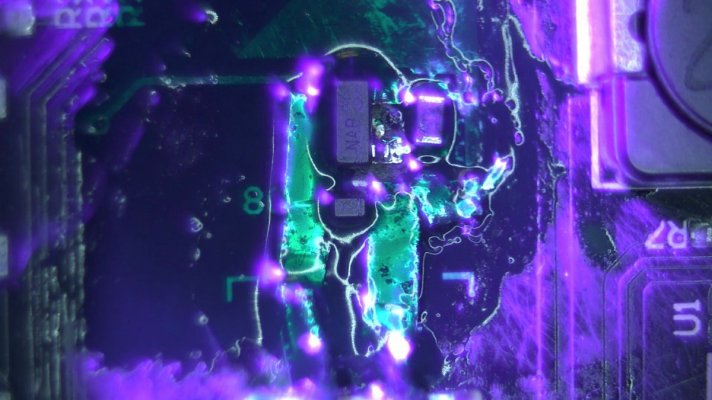
Once hardened, the conformal coating not only protects against corrosion, but also helps to hold my traces to the board.
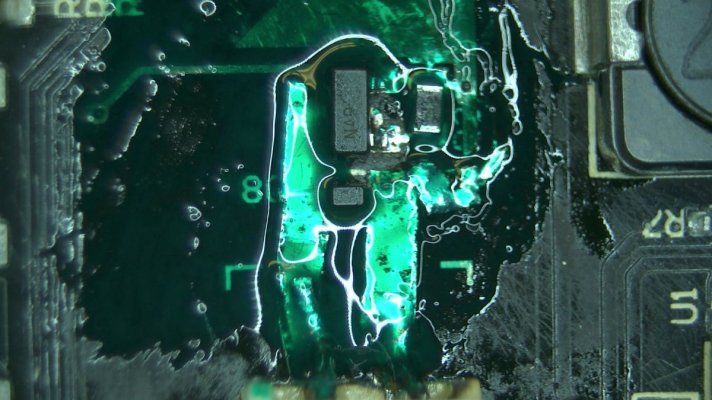
Now it's time to test if the new fan circuit actually works:
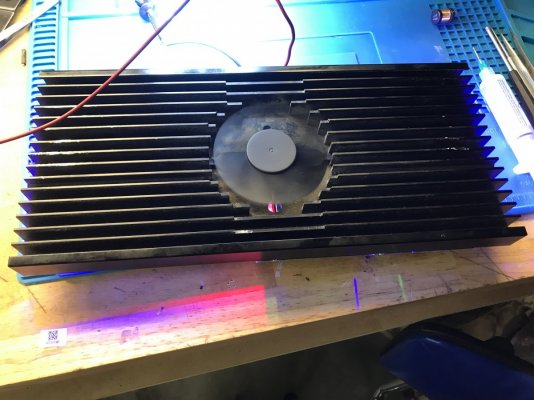
My leading theory on why the damage to the board was so significant is a sequence of events with the old fan failing and shorting first. The short caused a part of the circuit to burn out. You can actually see a small hole in the board right next to the diode where a part of the trace used to be. The short on the board made the black coating to flake off exposing copper on several traces. Copper usually corrodes violently, which might have been enough to push all the circuit components off the board.
Either way, the light is now working and the board circuit is corrosion resistant.